Warehouse picking strategies are crucial for optimizing efficiency, reducing costs, and increasing throughput in distribution centers. Zone picking and wave picking are widely implemented due to their effectiveness in different operational contexts. Understanding the nuances of each method can help warehouse managers make informed decisions about which strategy best suits their business needs. In this article, you will learn about Zone Picking vs. Wave Picking.
Zone Picking vs. Wave Picking
Zone picking and wave picking are two distinct strategies used in warehouse management to optimize the order fulfillment process. Zone picking involves dividing the warehouse into several zones, where each picker is assigned to a specific zone and is responsible for picking all the items within that area. This method is particularly effective in large warehouses with diverse inventories, as it minimizes the distance each picker travels, leading to increased efficiency and reduced picking time.
On the other hand, wave picking organizes the picking process into waves, scheduling specific times during which all orders or a group of orders are processed simultaneously. This method is well-suited for handling large volumes of orders with tight shipping deadlines, as it allows for the consolidation of shipping and can optimize the use of labor and equipment by aligning the picking activity with other warehouse operations like packing and shipping. Each strategy has its advantages and is best suited to different types of warehouse layouts and business needs.
What is Zone Picking?
Zone picking, also known as “pick and pass,” involves dividing the warehouse into different areas or zones. Each picker is assigned to a specific zone and is responsible for picking items only within that area. Items are then passed from one zone to the next until the order is complete. This method is highly effective in large warehouses with a diverse inventory, as it minimizes travel time and allows workers to become highly skilled and efficient in handling the specific products in their assigned zones.
Advantages of Zone Picking
- Efficiency in Large Operations: Zone picking reduces the distance each worker travels, as they stay within a specific area.
- Specialization: Workers can specialize in specific types of products, which can increase accuracy and speed.
- Scalability: Easily scalable during high demand periods by adding more workers to each zone without disrupting the workflow.
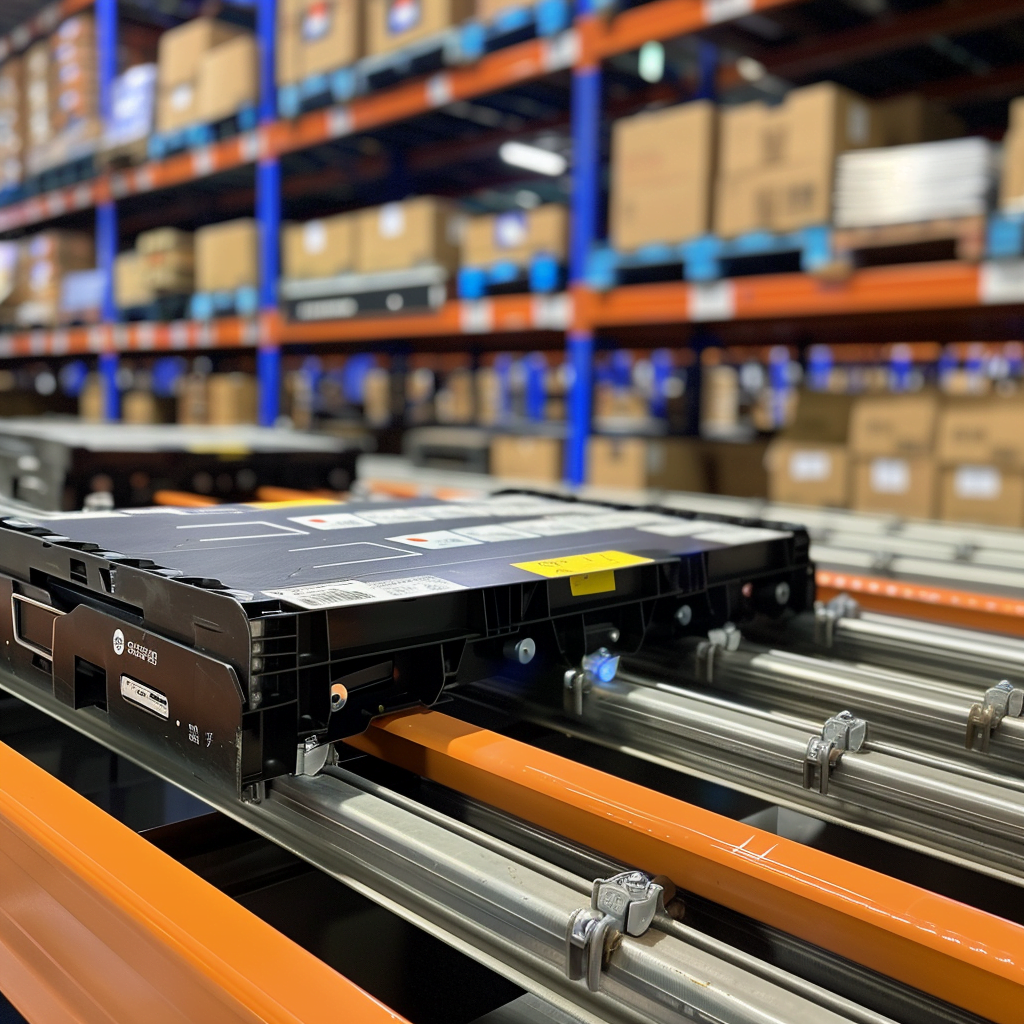
Challenges of Zone Picking
- Dependency: The process can be slowed down by delays in any zone, impacting overall efficiency.
- Complex Coordination: Requires effective communication and coordination between zones to ensure smooth transitions of items.
What is Wave Picking?
Wave picking is a method where orders are grouped into waves and picked at specific times throughout the day. Each wave is planned to optimize a combination of factors such as delivery schedules, shipping methods, and the type of merchandise. Wave picking can be used in conjunction with other picking methods, such as zone or batch picking, to further enhance efficiency.
Advantages of Wave Picking
- Order Consolidation: Allows for the consolidation of orders to optimize shipping, reducing transportation costs.
- Enhanced Planning: Enables better use of labor and equipment by scheduling waves based on the workload and deadlines.
- Flexibility: Suitable for operations that deal with varying order sizes and shipping urgencies.
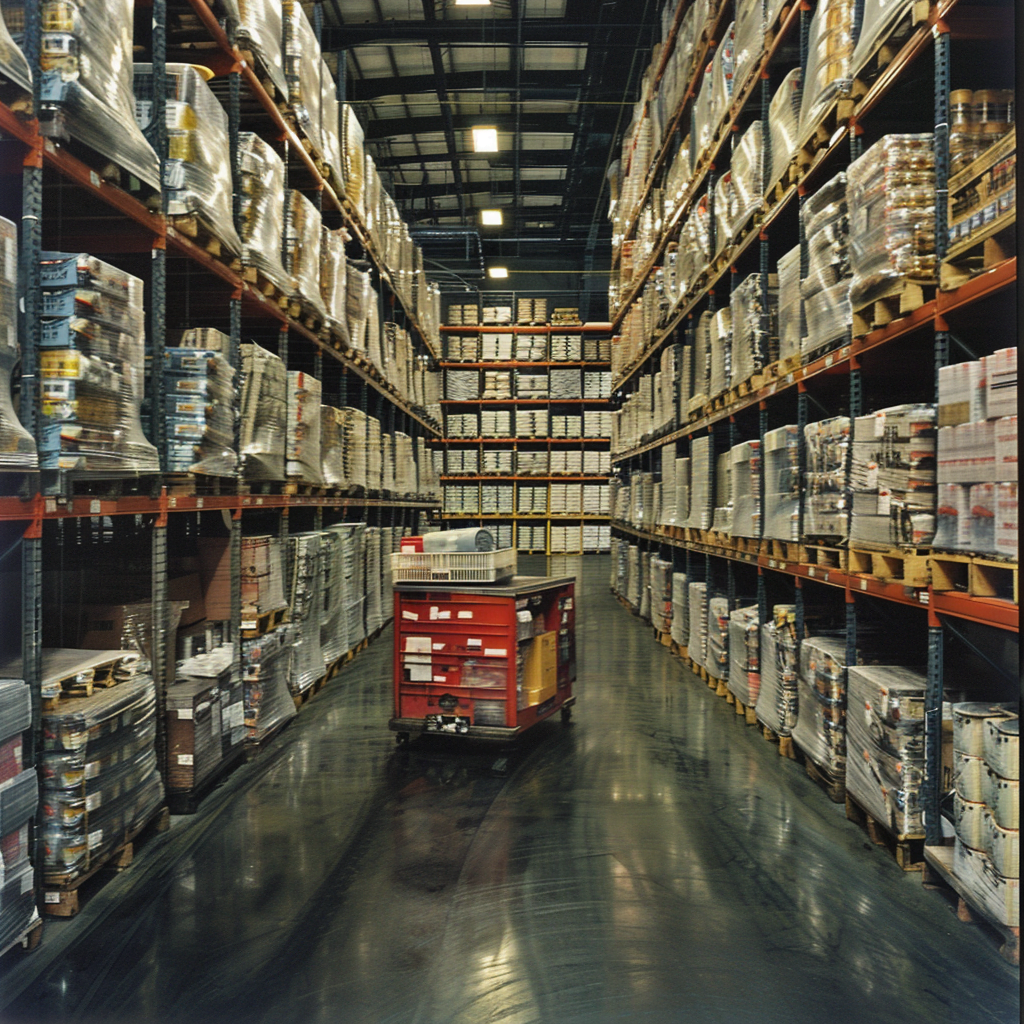
Challenges of Wave Picking
- Complex Planning: Requires sophisticated software and planning to efficiently manage the timing and resources of each wave.
- Potential Downtime: Workers may experience downtime between waves if not properly scheduled.
Suitability Comparison
- Zone Picking is more suited for larger warehouses with a high volume of SKUs and consistent order profiles, where specialization and minimizing walking time are beneficial.
- Wave Picking works best in environments where order shipping times vary and there is a need to synchronize with transportation schedules or manufacturing processes.
Efficiency Comparison
- Zone Picking optimizes picking efficiency by reducing travel time and increasing familiarity with product locations.
- Wave Picking enhances overall operational efficiency by aligning picking activities with other warehouse processes like packing and shipping.
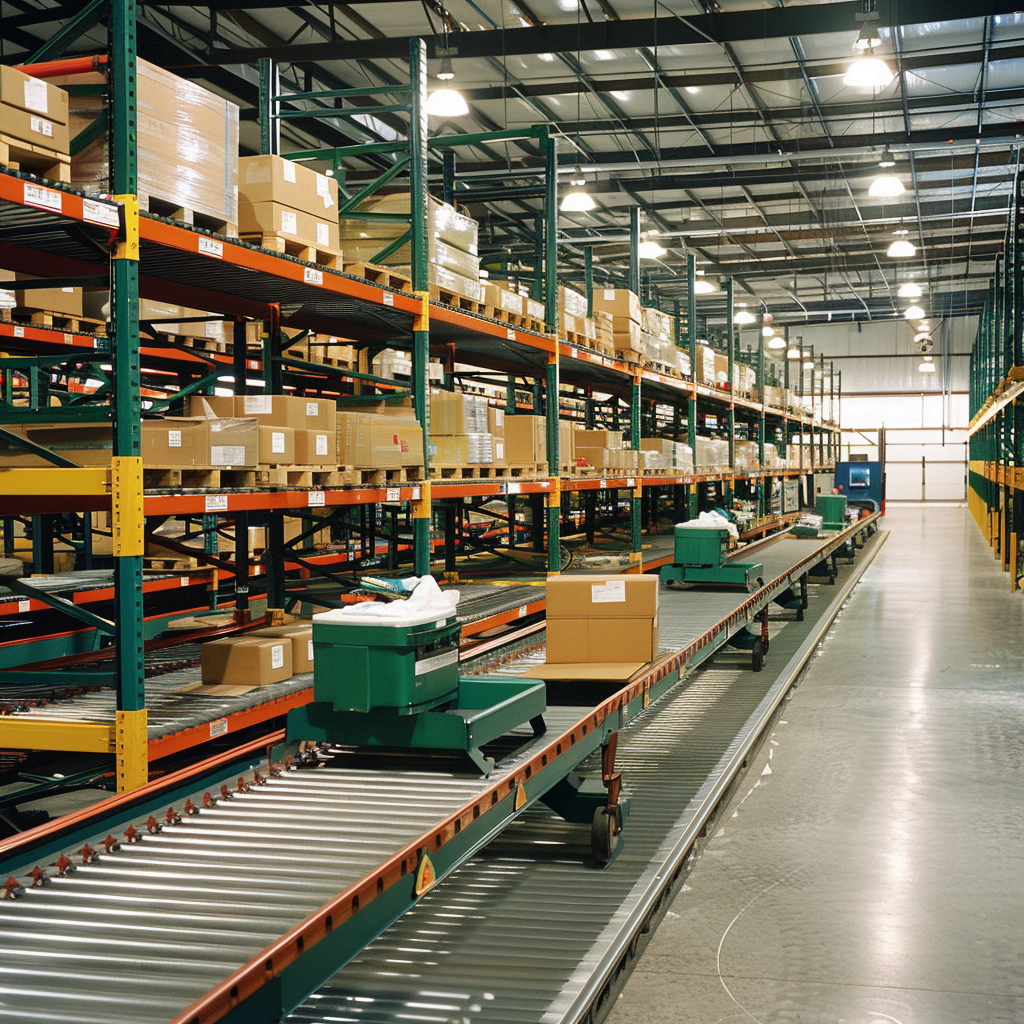
Scalability Comparison
- Zone Picking scales easily by adding more pickers to zones as needed.
- Wave Picking requires careful planning and resource allocation to scale effectively, especially in maintaining balance during peak periods.
Integration with Other Systems
Both picking methods can often be integrated with warehouse management systems (WMS) to enhance visibility and control over inventory, further improving efficiency and reducing errors.
Future Trends in Picking Strategies
As technology evolves, both zone and wave picking might see enhancements through automation, such as the use of robots and AI, making these methods even more efficient and adaptable to changing market demands.
Frequently Asked Questions About Zone Picking and Wave Picking
What is the main difference between zone picking and wave picking?
The main difference lies in the organization and execution of tasks. Zone picking divides the warehouse into distinct areas where pickers are responsible only for those zones, minimizing movement and increasing efficiency in handling specific items. Wave picking, on the other hand, organizes order picking into waves or batches at specific times to optimize shipping and delivery schedules, making it ideal for varying order sizes and urgent deliveries.
Which picking method is faster, zone picking or wave picking?
The speed depends on the specific needs and setup of the warehouse. Zone picking can be faster for larger warehouses with a diverse inventory as it reduces travel time and improves item handling efficiency. Wave picking can be faster in environments where order grouping and scheduled dispatches align well with workflow, allowing for streamlined operations during peak times.
Can zone picking and wave picking be used together?
Yes, these methods can be integrated to leverage the strengths of both. For example, a warehouse can be divided into zones with items picked in waves within each zone. This hybrid approach can optimize both the specialization of zone picking and the scheduling efficiencies of wave picking.
What are the technological requirements for implementing these picking strategies?
Implementing these strategies often requires a robust warehouse management system (WMS) that can handle complex inventory tracking, order management, and scheduling. Advanced WMS software can help coordinate between different zones or manage the scheduling of waves, and integrate with other systems like transportation management systems (TMS) for end-to-end efficiency.
How do I decide which picking method is right for my warehouse?
The choice depends on several factors, including the size of the warehouse, the variety and volume of inventory, the consistency of order profiles, and the delivery requirements. Analyzing these factors can help determine which method—or combination of methods—will best suit your operational needs and goals.
Are there any specific industries or types of products that benefit more from one method over the other?
Zone picking is often preferred in industries where a wide variety of items are stored in large warehouses, such as retail and e-commerce. It allows for specialized handling of different product types. Wave picking is beneficial in industries like manufacturing or distribution, where delivery and production schedules need to be tightly synchronized.
What challenges might I face when implementing zone or wave picking?
Challenges include the need for high coordination and communication in zone picking to ensure smooth transitions between zones. In wave picking, the complexity of planning and the risk of downtime between waves can be challenging, requiring precise timing and resource allocation.
How can I minimize errors in zone or wave picking?
Minimizing errors can be achieved through training, enhanced WMS functionalities, and automation. Ensuring pickers are well-versed in the picking process, and using technology like RF scanning and automated picking aids can significantly reduce picking errors.
What are the latest trends in improving zone and wave picking efficiencies?
Trends include the integration of automated picking solutions such as robotic pickers and drones, AI for better demand forecasting and wave planning, and the use of IoT devices for real-time inventory tracking. These technologies can enhance the speed and accuracy of both picking methods.
Can small to medium-sized enterprises benefit from these picking strategies?
Absolutely! While the scale might differ, small to medium-sized enterprises can still benefit from the organizational improvements that zone and wave picking offer. Even on a smaller scale, these strategies can improve order accuracy, speed up fulfillment, and increase overall warehouse efficiency.
Conclusion
Choosing between zone picking and wave picking depends largely on the specific needs of the warehouse, including the nature of the inventory, the consistency of order profiles, and the required speed of delivery. Each method has its strengths and weaknesses, and the best choice may involve integrating both strategies to leverage their benefits fully. By understanding and applying the right picking strategy, warehouses can significantly improve their operations and better meet the demands of their customers.