When it comes to warehouse operations, maintaining forklifts in optimal condition is crucial for...
Full-service forklift maintenance designed to reduce downtime and costs.
Turnkey Forklift Maintenance
People – Equipment – Workflow
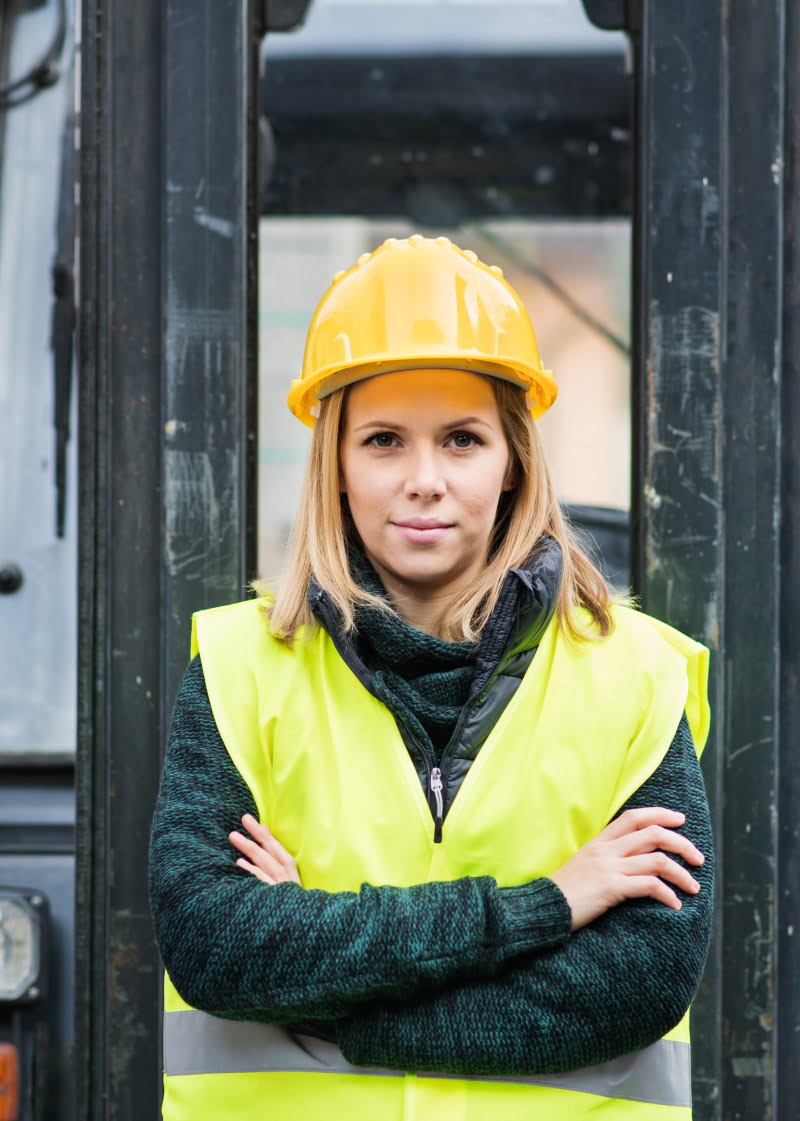
Turnkey forklift maintenance is a full-service solution designed to keep your fleet operational, safe, and efficient—without the hassle of managing repairs or scheduling service. It’s ideal for warehouse managers, operations directors, and fleet supervisors who need reliable uptime and expert support.
Our service programs are built around your operation’s needs and cover everything from routine inspections to emergency repairs. We manage the entire process so you can focus on productivity. Coverage typically includes:
- Scheduled preventative maintenance and inspections
- 24/7 emergency repair response
- On-site service and parts management
- Fleet tracking and maintenance reporting
- Custom service plans for electric, propane, and diesel forklifts
It’s a complete maintenance solution that saves time, reduces downtime, and extends equipment life.
Full-Service Forklift Maintenance Solutions for Maximum Uptime
Preventative Maintenance Plans
Emergency Repair Coverage
Customized Maintenance Programs
Learn More From Our Blog
How to Conduct a Forklift Maintenance Check
In the fast-paced world of warehouse operations, forklifts play a crucial role in moving goods...
The Impact of Forklift Maintenance on Fleet Efficiency
When it comes to warehouse operations, maintaining a fleet of forklifts is crucial for ensuring...
How to Optimize Forklift Maintenance for Different Models
When it comes to warehouse operations, efficient forklift maintenance plays a crucial role in...
The Role of Data Analytics in Forklift Maintenance
As warehouses continue to evolve and become more advanced, optimizing operations and ensuring...
How to Optimize Forklift Maintenance for High-Usage Environments
If you operate a warehouse or distribution center with a high-usage forklift fleet, you know how...
Why Choose HCO Innovations for Turnkey Forklift Maintenance?
When downtime costs money, you need a maintenance partner who delivers speed, consistency, and expertise. At HCO Innovations, we take full responsibility for keeping your forklifts in top condition—from routine service to emergency support. We handle everything so your team doesn’t have to.
- All-inclusive service contracts tailored to your operation
- Certified technicians for all major forklift brands
- Responsive emergency repair services to reduce downtime
- Fleet health tracking and performance reporting
- Simplified billing and a single point of contact
Our turnkey approach ensures your equipment runs efficiently, safely, and without interruption—so you can stay focused on moving your business forward.
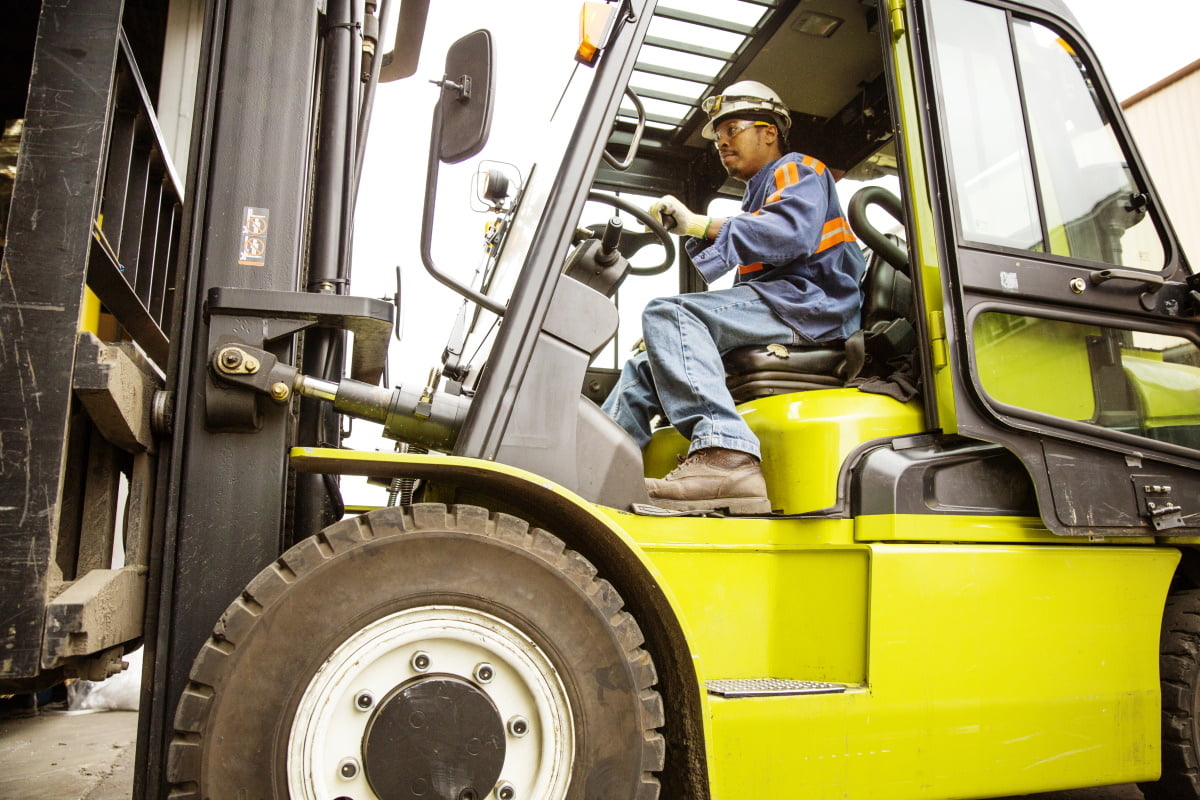