In the fast-paced and storage-intensive warehousing industry, effective space utilization is pivotal for operational efficiency and cost management. As companies face growing inventory levels and limited physical space, the challenge of optimizing storage without compromising accessibility and speed of operations becomes increasingly critical.
Understanding the Importance of Maximizing Space Utilization
Common Space Utilization Issues in Warehouses
Warehouses often grapple with issues such as cluttered layouts, inefficient use of vertical space, and outdated storage systems that hinder operational capabilities and scalability.
Strategic Planning for Layout Optimization
Assessing and planning the warehouse layout strategically is foundational for maximizing space utilization. This process starts with understanding the current setup and identifying areas for improvement.
Conducting Layout Analysis
Analyzing the current warehouse layout helps in pinpointing inefficiencies such as poorly placed aisles, underused areas, and inappropriately sized storage units, which can obstruct the flow of goods and workers alike.
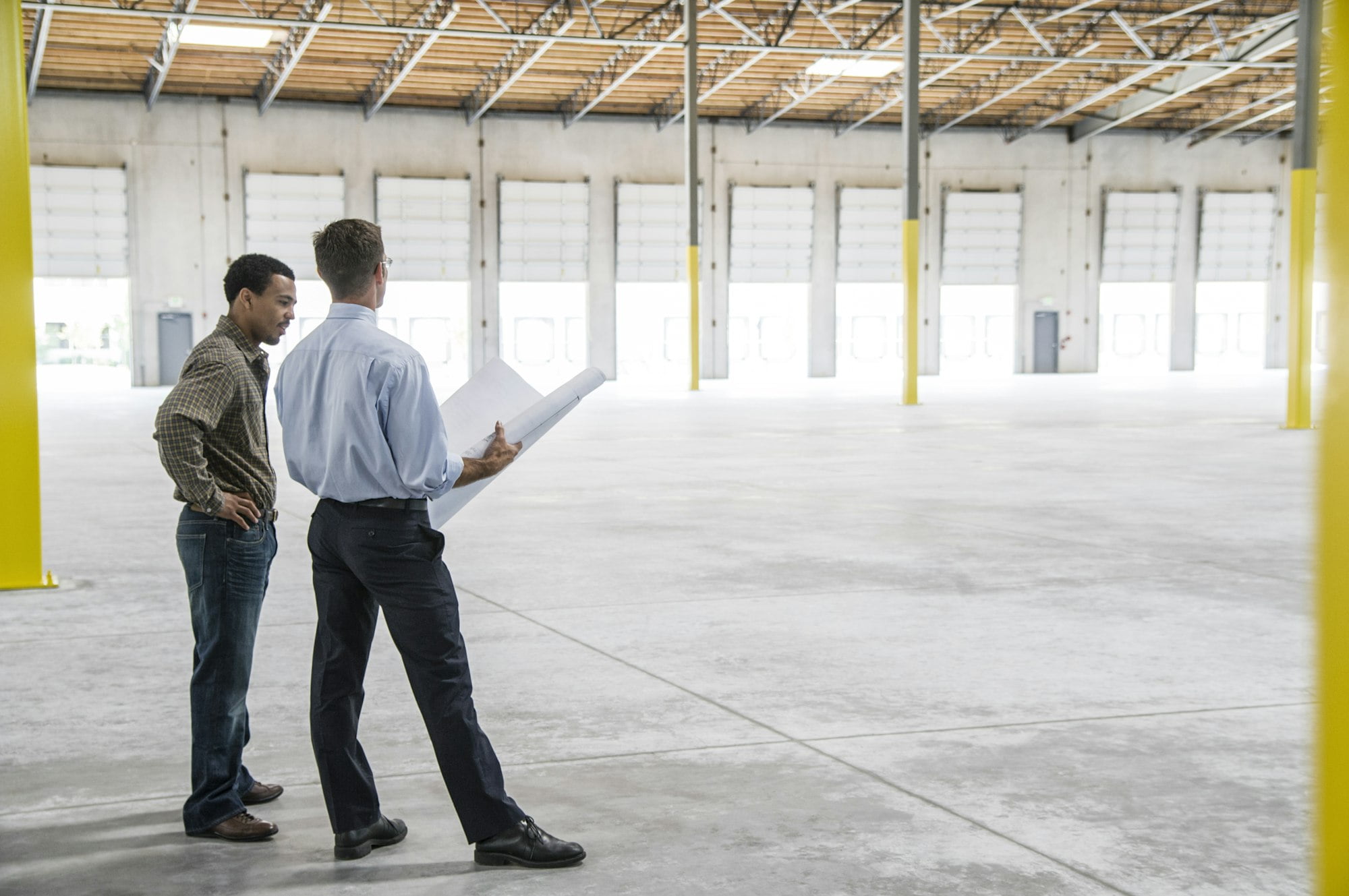
Back man owner of new warehouse and caucasian man architect going over blue print plans of new
Identifying Opportunities for Layout Improvement
Once areas of inefficiency are recognized, the next step is to reorganize, adjust, and potentially expand storage solutions vertically or through compact systems to better use the existing space.
Advanced Storage Solutions
Implementing advanced storage solutions can significantly boost space utilization. Choices range from multi-level racking systems to automated solutions that reduce the footprint and increase density.
Exploring Types of Racking Systems
Options like pallet racking, cantilever racking, and drive-in systems offer various benefits depending on the type of inventory and frequency of access required. Each system has its own strengths in terms of maximizing space and improving accessibility.
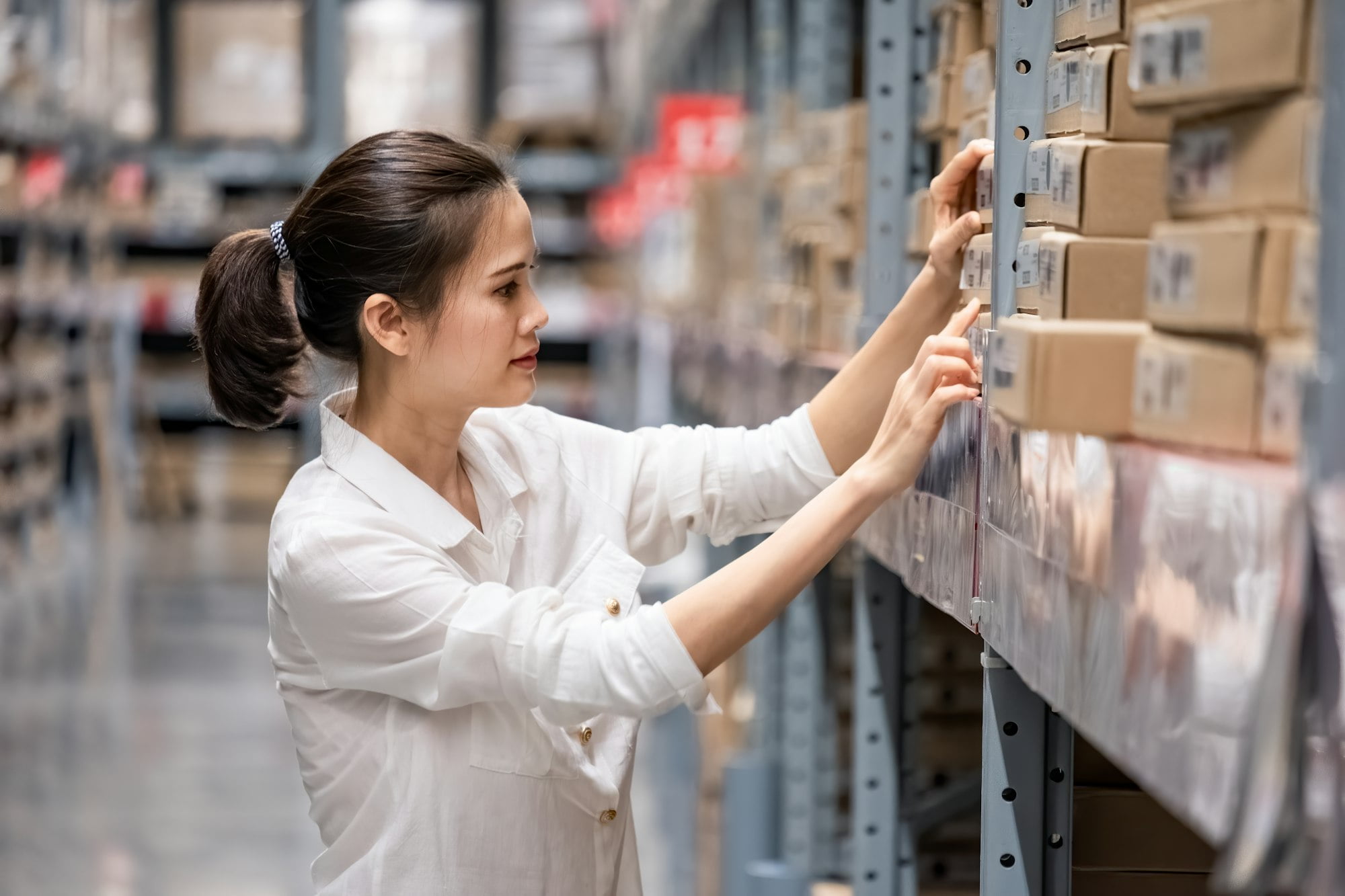
Smart Asian young woman happy to work in store warehouse.
Benefits of Vertical Storage Solutions
Vertical storage solutions take advantage of unused vertical space and can dramatically increase a warehouse’s capacity without extending its footprint, thus preserving valuable ground space for other operations.
Incorporating Mezzanine Floors to Increase Space
Mezzanine floors are an excellent option for expanding storage area vertically within the same warehouse footprint. They can be used for storage, as work areas, or to house operations offices, freeing up valuable ground-level space.
Technology Integration for Enhanced Efficiency
Integrating technology into warehouse operations can lead to significant improvements in space utilization and operational efficiency. Sophisticated systems like WMS and automated retrieval systems can transform the management of space.
Implementing Warehouse Management Systems
A robust Warehouse Management System (WMS) organizes inventory data, optimizes picking and placing processes, and reduces errors by automating tasks and providing real-time updates.
Role of Automation and Real-Time Data in Space Management
Automation technology, including robotics and conveyor systems, not only minimizes the need for extensive physical space but also enhances the accuracy and speed of operations, ensuring that space is used as efficiently as possible.
Efficient Inventory and Workflow Management
Effective inventory and workflow management are essential for optimizing space. By strategically managing stock levels and workflow, warehouses can significantly improve space utilization.
Adopting Just-In-Time Inventory Practices
Just-In-Time inventory practices reduce the need for large amounts of stock to be held on-site, thereby minimizing space requirements and associated costs.
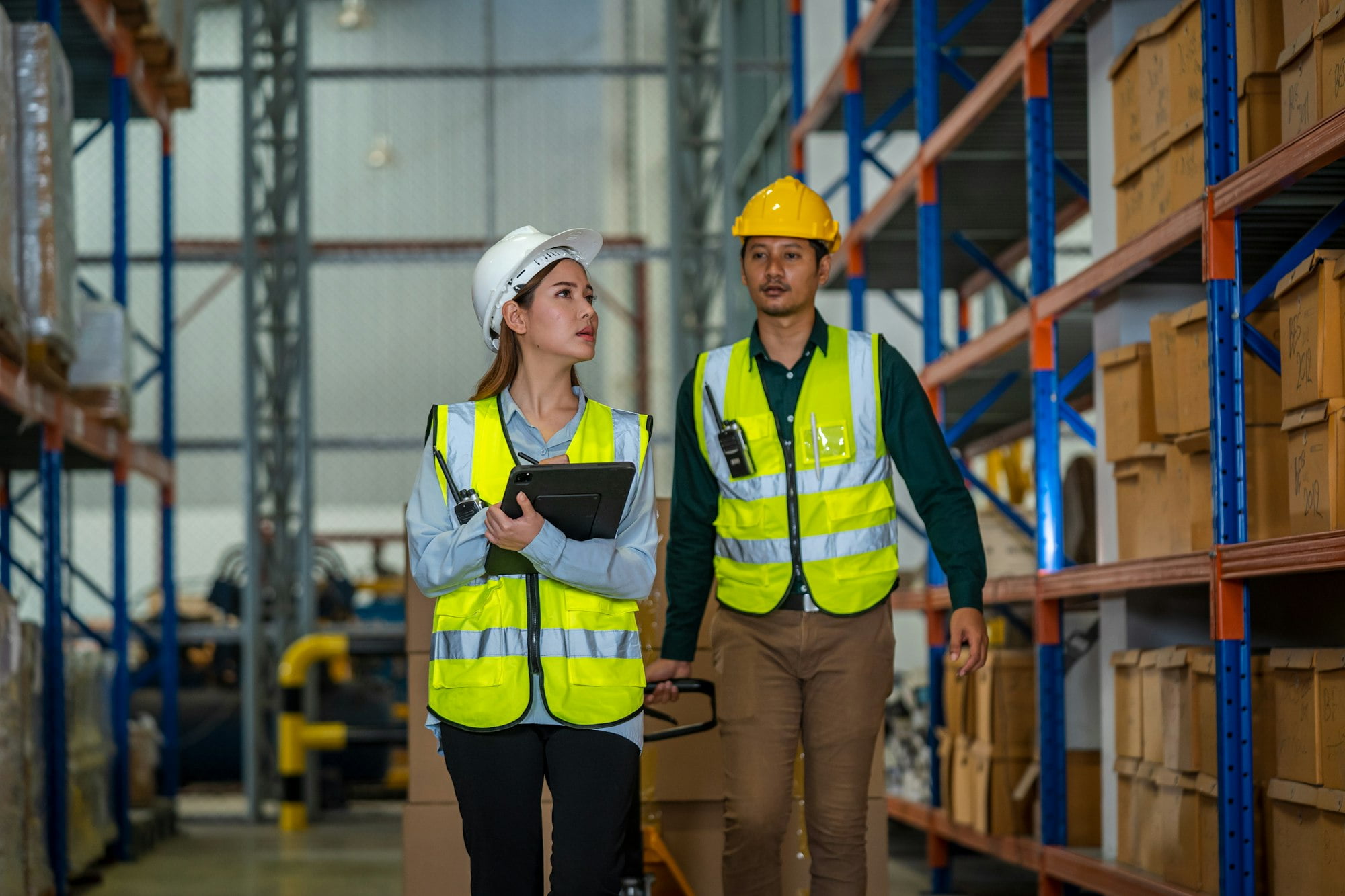
Warehouse employees with Inventory checking software in the retail warehouse.
Utilizing Cross-Docking to Minimize Storage Needs
Cross-docking allows goods to be directly transferred from incoming to outgoing trucks without storage in between, greatly reducing the space needed for inventory storage.
Dynamic Slotting for Optimizing Inventory Placement
Dynamic slotting adjusts storage locations based on changing inventory needs and sales patterns, which helps to use warehouse space more effectively and reduce picking times.
Optimizing Warehouse Infrastructure
Reevaluating and optimizing warehouse infrastructure, from the layout of aisles to the use of equipment, is crucial for maximizing space.
Streamlining Aisle Configurations
Optimizing aisle widths to accommodate material handling equipment can substantially increase storage space, allowing for tighter and more efficient storage configurations.
Selecting Appropriate Handling Equipment
Choosing the right material handling equipment that fits the warehouse layout and storage design is vital for
Optimizing Warehouse Infrastructure
Reevaluating and optimizing warehouse infrastructure, from the layout of aisles to the use of equipment, is crucial for maximizing space.
Streamlining Aisle Configurations
Optimizing aisle widths to accommodate material handling equipment can substantially increase storage space, allowing for tighter and more efficient storage configurations.
Selecting Appropriate Handling Equipment
Choosing the right material handling equipment that fits the warehouse layout and storage design is vital for efficient operations. This includes selecting forklifts and other machinery that can navigate narrower aisles and reach higher racks.
Regular Audits to Identify Space Wastage
Conducting regular audits helps identify and eliminate space wastage. This proactive approach ensures that the warehouse operates at optimal capacity by continuously adapting to changes in inventory and demand.
Enhancing Operational Procedures
Optimizing operational procedures is key to leveraging the full potential of warehouse space. This includes improving throughput and ensuring efficient flow of goods and personnel.
Improving Throughput and Material Handling
Enhancing throughput involves optimizing the movement and processing of goods within the warehouse. This includes streamlining procedures for receiving, storing, and shipping goods to minimize delays and reduce storage time.
Training Staff for Operational Efficiency
Training is crucial to ensure staff can operate effectively within an optimized space. Proper training on new equipment and layouts improves safety and efficiency, reducing errors and enhancing productivity.
Ensuring Accessibility and Safety in Layout Design
Warehouse layout must prioritize both accessibility and safety to maintain high levels of operational efficiency and worker satisfaction. Strategic placement of goods, clear signage, and easily navigable pathways contribute to a safer and more productive environment.
Future-Proofing Warehouse Operations
As business needs evolve, warehouses must adapt to remain competitive and efficient. Planning for future needs and integrating flexible solutions can safeguard against obsolescence and maintain operational efficiency.
Planning for Scalability and Flexible Layouts
Designing warehouses to be scalable and flexible allows for adjustments in layout and operations as business needs change. This could involve modular storage systems or reconfigurable layouts that can expand or contract as required.
Integrating Sustainable Practices and Waste Management
Implementing sustainable practices and effective waste management not only supports environmental goals but also enhances operational efficiency. Reducing waste and recycling materials can lead to cost savings and a stronger brand image.
Conclusion
In conclusion, maximizing warehouse space utilization involves a comprehensive approach that includes optimizing the layout, integrating technology, managing inventory efficiently, and enhancing operational procedures. By focusing on these key areas, warehouses can improve their operational efficiency, reduce costs, and prepare for future growth and challenges.
Summarizing Key Takeaways for Space Optimization
Effective space optimization strategies include layout reevaluation, technology integration, and dynamic inventory management. These strategies are essential for maximizing efficiency and scalability in warehouse operations.
Long-Term Benefits of Efficient Space Utilization
The long-term benefits of efficiently utilizing warehouse space extend beyond immediate cost savings. They include improved operational efficiency, reduced environmental impact, and enhanced ability to adapt to market changes and customer demands, ensuring sustained success.