Warehouse operations encompass a range of activities from inventory management to goods dispatch, and optimizing these processes is vital for maintaining competitive advantage. Effective warehouse management ensures that goods are stored, picked, and transported efficiently, which minimizes costs and improves service delivery. This article explores various strategies to streamline operations and enhance the functional prowess of warehouse settings.
Warehouse Operations
Warehouse operations encompass the entire process of managing the storage, handling, and movement of goods within a warehouse environment, from receiving and storing to picking, packing, and shipping products. Effective management of these operations is critical for businesses to ensure timely delivery of products, optimize inventory levels, and maintain customer satisfaction. As commerce continues to evolve with increasing emphasis on speed and efficiency, optimizing warehouse operations becomes even more crucial.
This involves implementing advanced technological solutions, adopting efficient inventory management practices, and ensuring that the warehouse layout is designed to maximize productivity and reduce waste.
Essentials of Order Fulfillment for Enhanced Speed and Accuracy
Optimizing order fulfillment involves refining picking methods and incorporating technology to speed up operations and increase accuracy. Strategies such as zone picking and advanced systems like pick-to-light can significantly reduce errors and improve throughput.
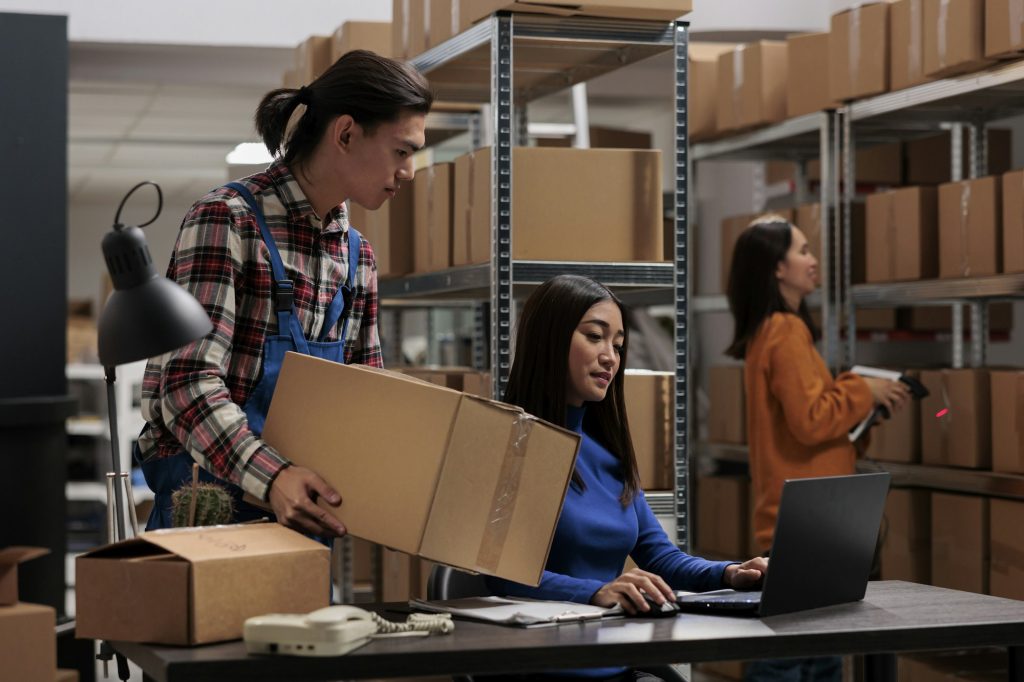
These enhancements not only streamline processes but also bolster customer satisfaction by ensuring faster and more reliable deliveries.
Strategic Preparations for High-Demand Periods
Preparing for peak seasons requires a proactive approach to inventory and labor management. Anticipating demand through robust forecasting models enables warehouses to allocate resources effectively, ensuring they can handle surges in orders without compromising on delivery times or accuracy. Such preparedness is crucial for maintaining service quality during critical periods.
Advanced Strategies for Warehouse Efficiency
Increasing warehouse efficiency often involves adopting lean principles and continuous improvement practices. Tools and methodologies that promote efficiency include the 5S system, which organizes and maintains productive work environments, and kaizen, a strategy focused on incremental improvements.
Implementing Lean Warehousing with Just-In-Time Inventory Systems
Just-In-Time (JIT) inventory systems reduce waste and inventory costs by receiving goods only as needed. Integrating JIT with material flow evaluations supports lean warehousing by ensuring that inventory levels are tightly controlled and aligned with production schedules, minimizing excess stock and storage costs.
Design Principles for Efficient Warehouse Layouts
The design of a warehouse significantly impacts its efficiency. Effective layout planning considers the balance between space utilization and the flexibility to adapt to changing business needs. Strategic placement of high-demand items and efficient traffic flow paths can reduce picking times and enhance operational agility.
Optimization Techniques for Small and Narrow Warehouse Spaces
Optimizing small or constrained warehouse spaces involves utilizing vertical storage and compact shelving systems to maximize available area.
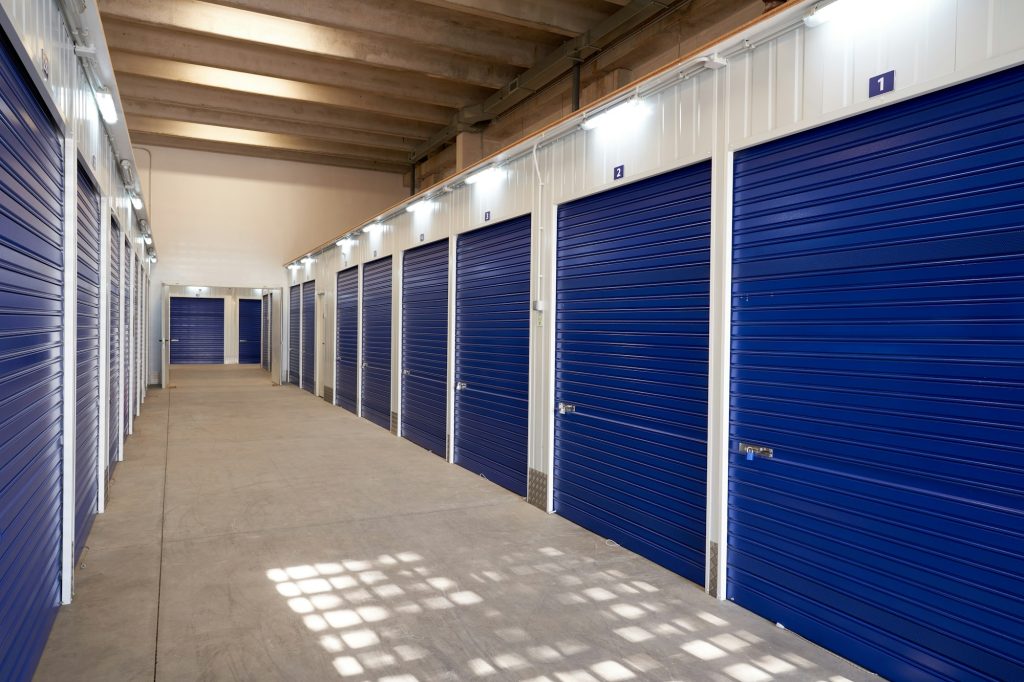
Specialized material handling equipment, such as narrow aisle forklifts, also plays a critical role in enhancing the use of limited spaces without sacrificing efficiency.
Principles for Maximizing Warehouse Space Utilization
Maximizing warehouse space utilization requires innovative storage solutions and dynamic layout designs. Implementing modular storage systems and adjustable racking can help accommodate varying inventory sizes and volumes, thus optimizing the use of warehouse space.
Methodologies for Crafting Efficient Warehouse Layouts
Crafting efficient warehouse layouts involves detailed planning and the use of digital tools to simulate and test different configurations. This approach allows for the identification of the most effective layout based on specific operational requirements and can significantly enhance overall workflow.
Techniques for Comprehensive Warehouse Layout Evaluations
Regular assessments of warehouse layouts are essential for maintaining operational efficiency. These evaluations should include analysis of workflow, space utilization, and accessibility to identify areas for improvement. Implementing changes based on these evaluations can lead to substantial enhancements in operational performance.
Integrating Advanced Technology Solutions in Warehouse Operations
The integration of advanced technologies such as robotics, artificial intelligence, and the Internet of Things (IoT) can transform traditional warehouse operations. These technologies improve accuracy, reduce labor costs, and streamline operations, making warehouses smarter and more responsive to the demands of modern commerce.
Enhancing Warehouse Operations with AI and Automation
Artificial intelligence (AI) and automation are revolutionizing warehouse operations by optimizing tasks such as inventory management, routing, and scheduling. These technologies not only improve efficiency but also enhance the ability to predict and respond to operational challenges quickly.
Improving Labor Management in Warehouse Settings
Effective labor management is key to operational success in warehouses. Implementing systems that track performance and productivity helps managers make informed decisions that enhance labor efficiency and reduce costs.
Effective Inventory Management and Control
Robust inventory management systems are crucial for ensuring that stock levels are maintained appropriately and that orders are fulfilled accurately. Advanced inventory solutions provide real-time data that aids in making informed decisions about stock handling and order processing.
Environmental Considerations and Sustainability in Warehouse Management
Warehouses play a significant role in sustainability efforts within supply chains. Implementing practices that reduce energy consumption and waste production not only supports environmental goals but also leads to cost savings and improved public perceptions.

Strategies such as optimizing energy use, reducing material waste, and incorporating green technologies are becoming standard practices in modern warehouse operations.
Conclusion and Future Trends in Warehouse Optimization
As the demand for faster and more efficient supply chain solutions continues to grow, the role of warehouse operations in achieving these goals becomes increasingly significant. Future trends in warehouse optimization are likely to focus on further automation, enhanced real-time data integration, and increased use of artificial intelligence to predict supply chain disruptions before they occur. Embracing these advancements will not only streamline operations but also elevate the strategic role of warehouses in global commerce.