In many modern warehouses, maximizing space while maintaining efficiency in inventory management and logistics has led to the development of narrow aisles. These aisles, typically ranging from 6 to 10 feet in width, are a strategic response to increasing demand for storage within limited spaces. This section explores the fundamental aspects of narrow aisle configurations, the historical development of warehouse layouts, and the influence of aisle width on operational efficacy.
What Constitutes a Narrow Aisle
A narrow aisle is defined primarily by its width, which is less than half that of traditional aisles. This reduction in space necessitates specialized equipment and operational strategies to effectively manage product storage and retrieval.
Historical Evolution of Warehouse Layouts
Over the decades, technological advancements and the growing need for more efficient space utilization have influenced the evolution of warehouse layouts. From sprawling single-story buildings with wide aisles to multilevel complexes featuring narrow passageways, the architectural design of warehouses has transformed significantly.
Comparative Analysis of Aisle Widths and Their Impacts
The width of an aisle in a warehouse directly affects both the type of machinery that can be used and the speed at which operations can be conducted. Narrower aisles require more precise handling but offer the benefit of a higher density of storage space.
Technological Solutions for Narrow Aisles
Adapting to the challenges of narrow aisles involves the deployment of advanced technological solutions. This section covers the essential equipment tailored for narrow environments, dives into the specifications of narrow aisle forklifts, and discusses innovations in warehouse navigation systems that contribute to operational success.
Overview of Equipment Designed for Narrow Aisles
Equipment such as turret trucks reach trucks, and stand-up counterbalance forklifts are specifically designed for operation in narrow aisles. These machines are engineered to offer excellent maneuverability and vertical reach capabilities.
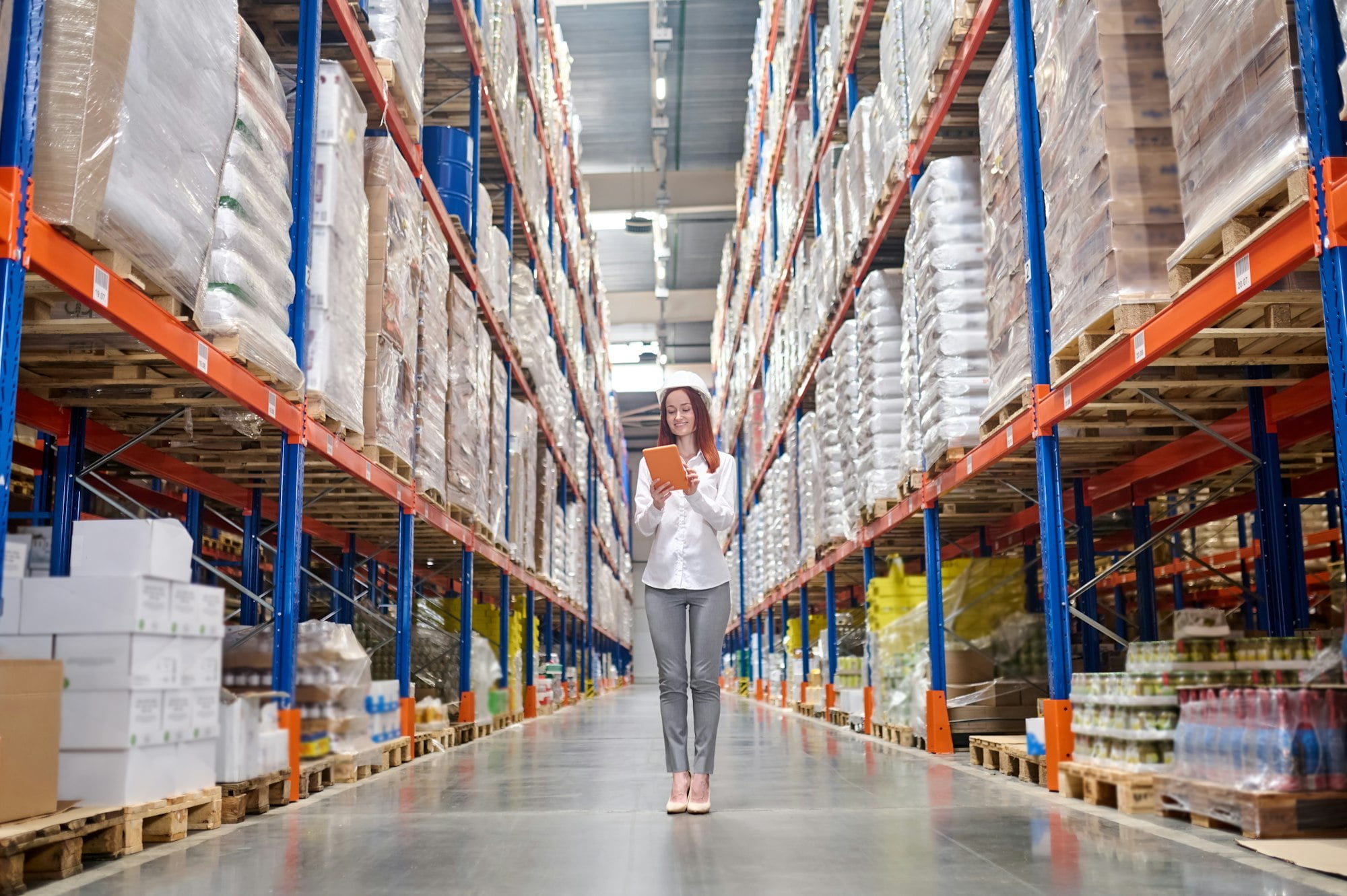
Elegant woman with tablet standing in warehouse aisle
Technical Specifications of Narrow Aisle Forklifts
Narrow aisle forklifts are typically equipped with features that allow for safe and efficient operation in confined spaces. Specifications such as a tighter turning radius, advanced lift controls, and narrower chassis are common among these vehicles.
Innovations in Warehouse Navigation Systems
Modern warehouses often employ sophisticated navigation systems that guide machinery and operators through optimal paths, reducing the time taken for inventory tasks and enhancing overall safety.
Optimizing Operations in Narrow Aisles
To fully leverage the potential of narrow aisles, operational strategies must be refined. This involves enhancing storage capacity, improving maneuverability, and reducing costs through efficient equipment use.
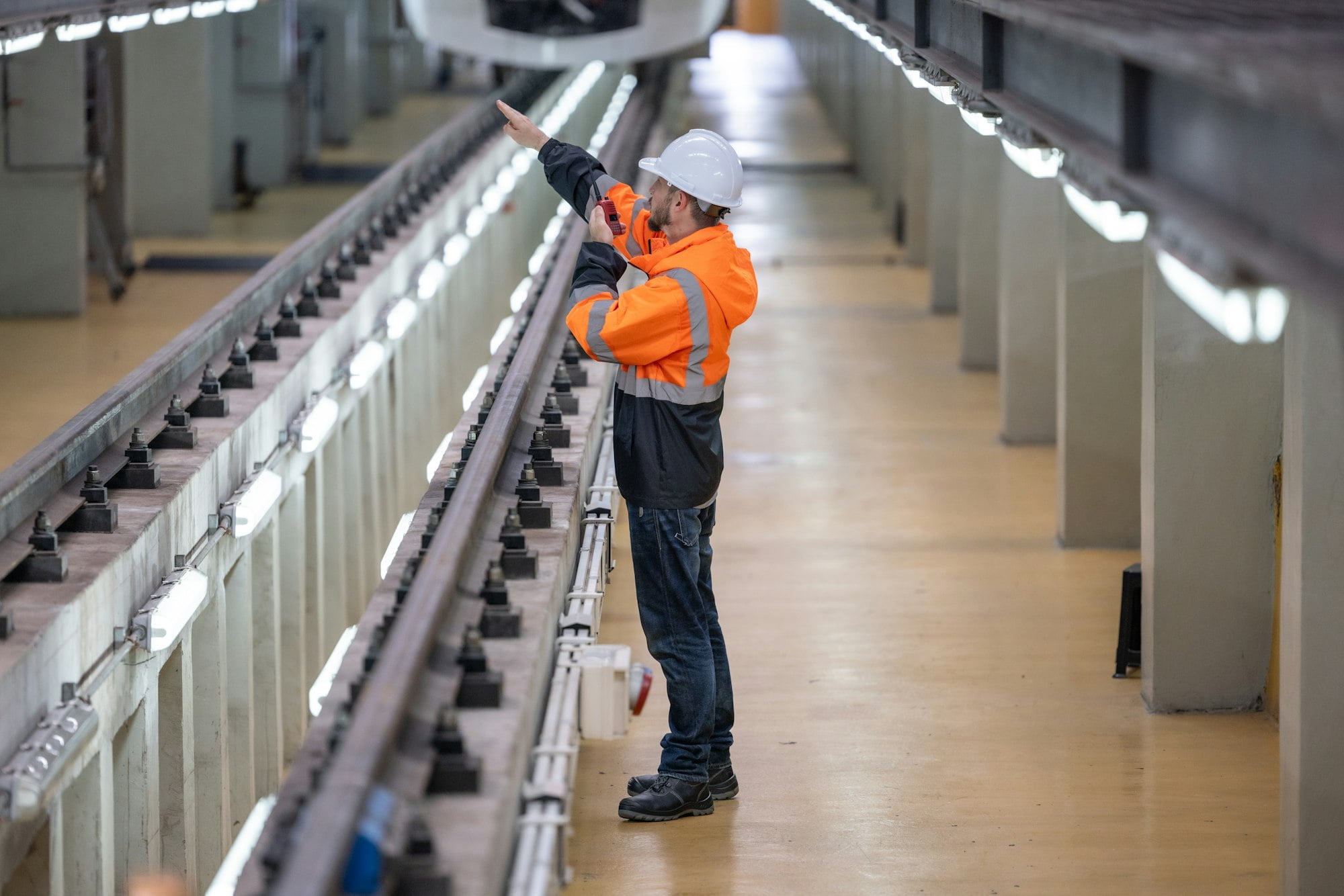
Rail engineer check and optimize overall infrastructure for energy efficient, green operations.
Strategies for Enhancing Storage Capacity
One key strategy is the vertical expansion of storage racks which can be accessed by high-reaching forklifts designed for narrow aisle work.
Tactics for Improving Maneuverability
Implementing a warehouse management system (WMS) can drastically improve the maneuverability of equipment by scheduling and routing operations to minimize congestion and streamline movement.
Cost Reduction through Efficient Equipment Use
Choosing the right machinery and maintaining it properly reduces breakdowns and operational delays, thereby minimizing costs associated with downtime and repairs.
Equipment Selection for Narrow Aisles
Selecting the appropriate equipment for narrow aisles is crucial for optimizing warehouse operations. This section provides guidelines on choosing the right forklift, offers a comparative analysis of popular models, and addresses the need to adapt equipment for specific warehouse environments.
Criteria for Selecting the Right Forklift
Key criteria include the forklift’s lift capacity, maneuverability, energy efficiency, and compatibility with the warehouse’s dimensions and operational style.
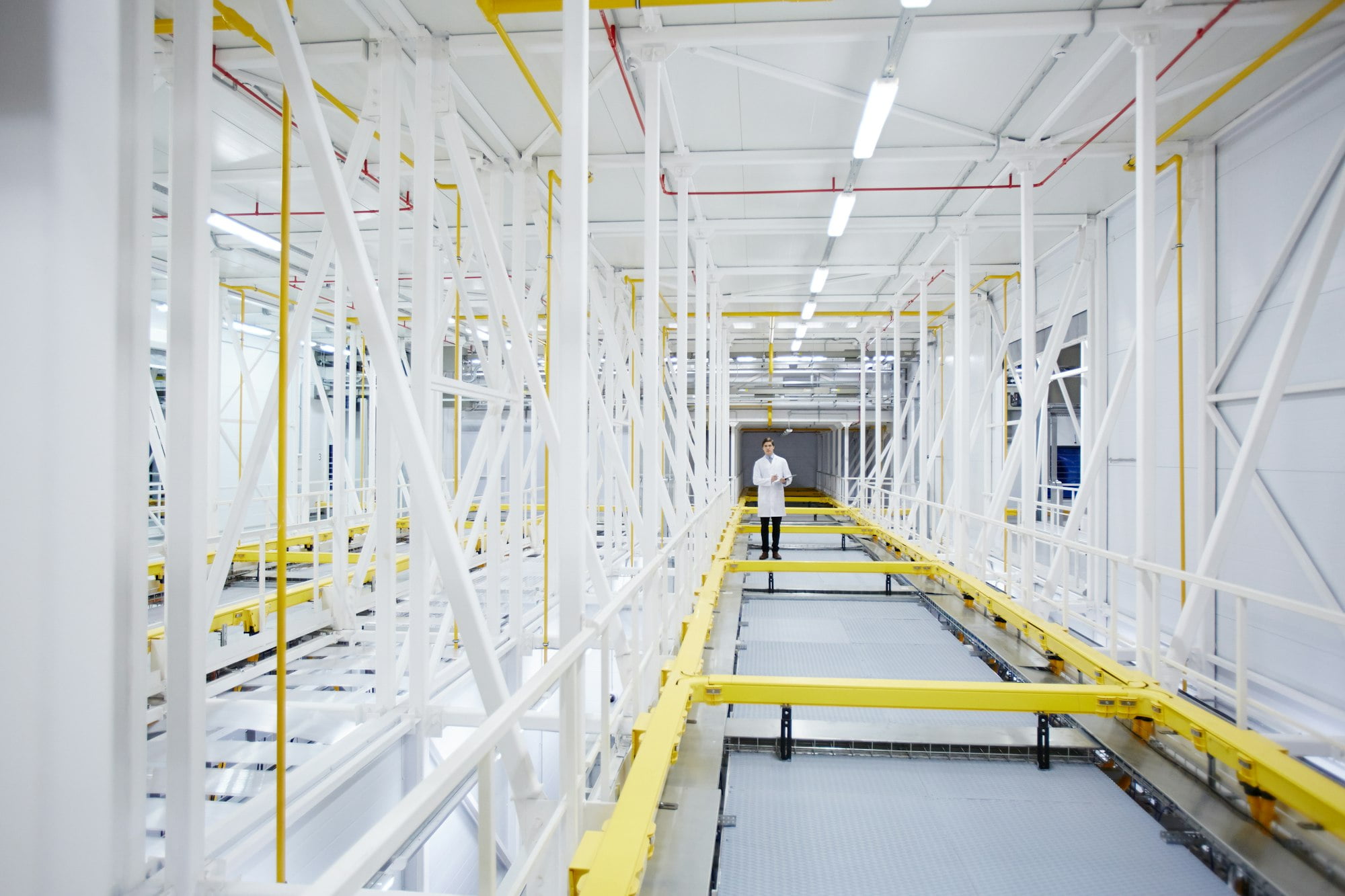
Aisle in mining farm
Detailed Comparison of Popular Models
A detailed comparison of various forklift models helps decision-makers understand which features align best with their operational needs and budget constraints.
Adapting Equipment for Specific Warehouse Needs
Customizing equipment to fit specific warehouse environments can greatly improve efficiency. This may involve modifications to handling capacity, lift heights, and even the software systems used in warehouse operations.
Enhancing Safety in Narrow Aisle Environments
Operating in narrow aisles raises certain safety concerns that must be addressed through stringent safety protocols, comprehensive training programs, and proactive risk management.
Key Safety Protocols for Operations
Establishing and enforcing strict safety protocols, such as clear
Key Safety Protocols for Operations
Establishing and enforcing strict safety protocols, such as clear aisle marking, proper lighting, and regular safety audits, is essential. These measures help prevent accidents and ensure a secure environment for warehouse personnel.
Mandatory Training and Certifications for Operators
Operators of narrow aisle forklifts must undergo specialized training to handle the specific challenges posed by narrow spaces. Certification programs not only comply with legal requirements but also enhance operator skill levels, contributing to safer warehouse operations.
Methods to Identify and Mitigate Risks
Risk assessment tools and continuous monitoring are crucial for identifying potential hazards. Implementing measures such as sensor-based systems can prevent collisions and ensure safe navigation through narrow passages.
Practical Insights and Case Studies
Real-world applications of theories and strategies provide valuable insights into the practical aspects of navigating narrow aisles. This section delves into case studies that showcase effective solutions and discusses the challenges and lessons learned from various industry leaders.
Case Studies Highlighting Effective Solutions
Exploring case studies from sectors like retail and distribution provides a concrete understanding of how businesses effectively manage their narrow aisle spaces. These examples demonstrate the application of best practices in real scenarios.
Challenges Faced and Overcome in Real Settings
Discussing specific challenges faced by warehouses and how they were addressed reveals critical strategies that can be applied universally. This includes optimizing layout designs and integrating advanced technological systems.
Lessons Learned from Industry Leaders
Insights from industry leaders offer a deep dive into the strategic thinking and continuous improvement processes that underlie successful narrow aisle management.
Future Directions in Aisle Management
Looking ahead, the management of narrow aisles is poised to evolve further as technology advances and warehouse demands increase. This section forecasts trends and anticipates changes in industry standards, exploring how upcoming innovations could reshape aisle management strategies.
Emerging Trends in Warehouse Design
Emerging trends, such as automation and robotic systems, promise to enhance the functionality of narrow aisles, increasing efficiency while reducing the need for manual intervention.
Anticipating Changes in Industry Standards
As the industry grows, standards evolve to reflect new safety, efficiency, and technological benchmarks. Anticipating these changes allows businesses to stay compliant and competitive.
Technological Advances on the Horizon
The future of warehouse management will likely see the integration of AI and machine learning, improving the precision and efficiency of operations in narrow aisles. These technologies are expected to offer solutions that could dramatically transform how warehouses operate.
Concluding Thoughts
This guide has explored the essential aspects of navigating narrow aisles, from understanding the basics to anticipating future trends. Strategically applying this knowledge can significantly enhance the efficiency and safety of warehouse operations.
Recap of Key Techniques and Strategies
This recap summarizes the main techniques and strategies discussed and reinforces the importance of appropriate equipment selection, safety protocols, and innovative solutions in mastering narrow aisle navigation.
Final Recommendations for Warehouse Managers
To optimize their operations, warehouse managers are encouraged to continuously evaluate and adapt their strategies based on the latest industry developments and technological advancements.