In today’s highly competitive market, efficient warehouse management is crucial for businesses looking to improve their operational efficiency and reduce costs. Lean warehousing integrates lean principles, originally developed in the manufacturing sector, into warehouse operations. This method focuses on eliminating waste, optimizing processes, and continuously improving productivity. In this comprehensive guide, we will explore the core principles, benefits, and best practices of lean warehousing to help you enhance your warehouse operations.
What is Lean Warehousing?
Lean warehousing is a systematic approach to managing warehouse operations by focusing on reducing waste, improving efficiency, and enhancing productivity. It is based on the principles of lean manufacturing, which were pioneered by Toyota in the mid-20th century. These principles have been adapted to fit the unique needs of warehouse environments, helping businesses streamline their operations, reduce costs, and improve customer satisfaction.
Core Principles of Lean Warehousing
The core principles of lean warehousing revolve around the 5S system, technology integration, continuous improvement, best practices, and employee involvement. Let’s explore each of these principles in detail.
The 5S System
The 5S system is a set of principles that help organize and manage the warehouse environment to improve efficiency and reduce waste. The five principles are:
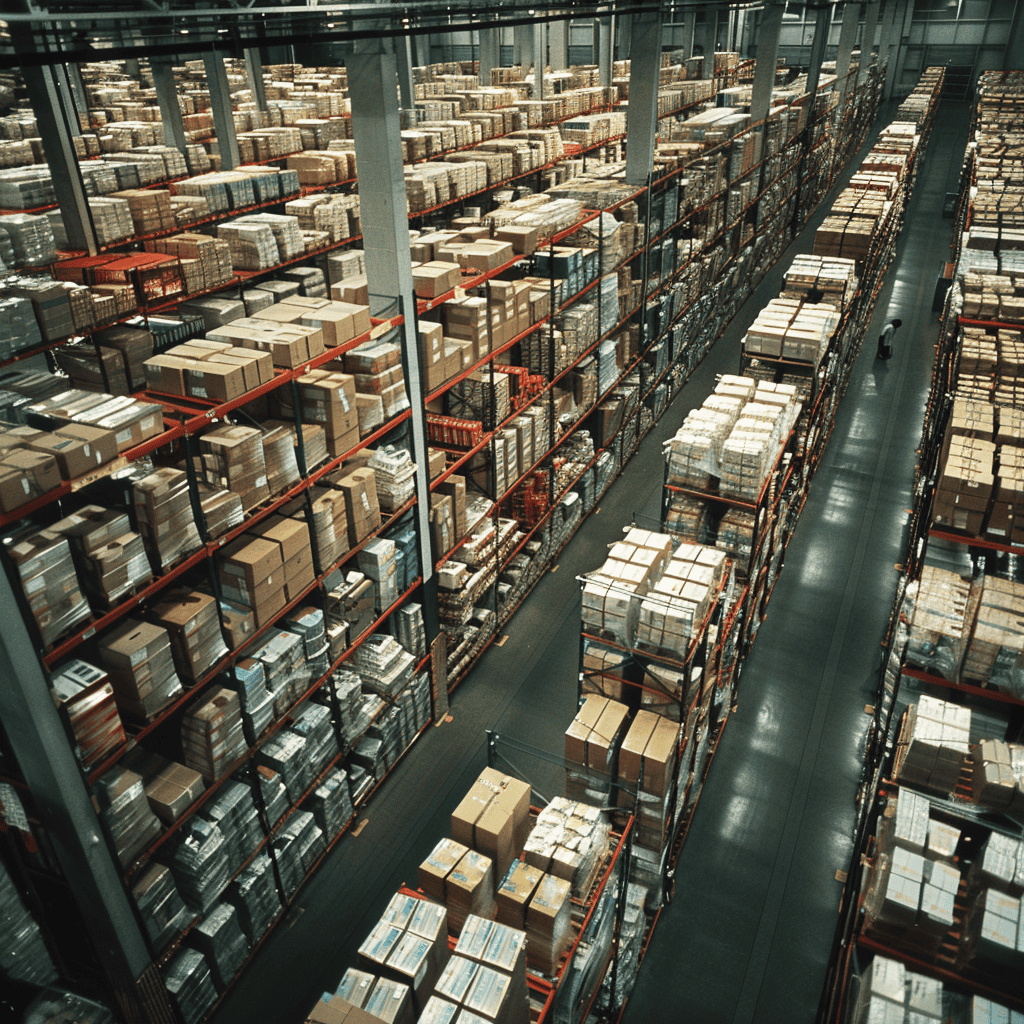
- Sort (Seiri): This principle involves removing unnecessary items from the warehouse to free up space and reduce clutter. Items that are not frequently used or are obsolete should be discarded or stored in a separate area.
- Set in Order (Seiton): This principle focuses on organizing items so that they are easy to find and access. Items should be stored based on their frequency of use, with frequently used items placed in easily accessible locations.
- Shine (Seiso): Maintaining a clean and well-organized warehouse is crucial for promoting safety and efficiency. Regular cleaning and maintenance routines should be established to keep the warehouse in optimal condition.
- Standardize (Seiketsu): Consistent processes and procedures should be established and followed to maintain efficiency. This includes documenting workflows, inventory management practices, and order fulfillment procedures.
- Sustain (Shitsuke): The first four principles should be continuously maintained and improved upon. Regular audits, employee training, and fostering a culture of continuous improvement are essential for sustaining lean practices.
Technology Integration
Technology plays a crucial role in lean warehousing by automating time-consuming activities and minimizing manual processes. Key technologies include:
- Warehouse Management Systems (WMS): These systems provide better visibility into warehouse operations and inventory, allowing for efficient control and management from a single platform. They help reduce errors, optimize storage, and improve order fulfillment processes.
- Automation and Robotics: Implementing automation can streamline processes and reduce the need for manual labor. Automated systems like vertical lift modules and automated sorting systems can significantly enhance efficiency.
Continuous Improvement
Lean warehousing is not a one-time effort but a continuous process of evaluating and improving operations. Regular audits, employee training, and fostering a culture of continuous improvement are crucial to sustaining lean practices.
Best Practices in Lean Warehousing
Adopting best practices can help maximize the benefits of lean warehousing. Some key practices include:
- Cross-Docking: This practice involves transferring goods directly from incoming to outgoing shipments, minimizing storage time and handling costs.
- Inventory Management: Regularly re-evaluating inventory levels and implementing a just-in-time system can reduce excess inventory and associated costs.
- Utilizing Lean Tools: Tools such as 5S, Kaizen, and Value Stream Mapping can help identify and eliminate waste in the warehouse.
Employee Involvement
Encouraging employee input and creativity is essential for identifying inefficiencies and developing innovative solutions. A collaborative approach helps build a culture of continuous improvement and employee empowerment.
Benefits of Lean Warehousing
Implementing lean warehousing principles can bring numerous benefits to businesses, including:
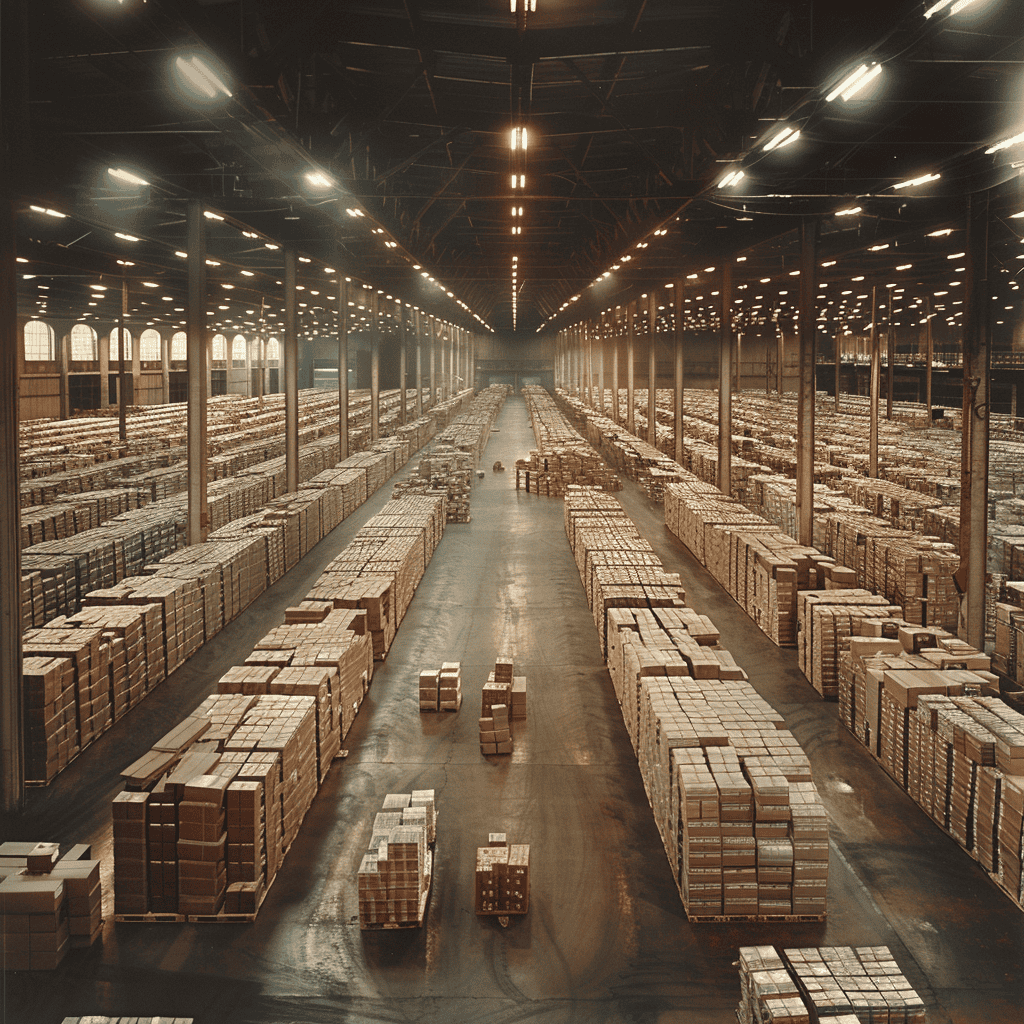
- Reduced Operational Costs: By eliminating waste and optimizing processes, businesses can significantly reduce their operational costs.
- Improved Efficiency: Streamlined processes and the use of technology can enhance overall warehouse efficiency, leading to faster order fulfillment and reduced lead times.
- Enhanced Customer Satisfaction: Faster and more accurate order fulfillment leads to higher customer satisfaction and loyalty.
- Better Space Utilization: Efficient organization and storage solutions help maximize the use of available warehouse space.
- Higher Employee Morale: A clean, organized, and efficient work environment boosts employee morale and job satisfaction.
Implementing Lean Warehousing
To successfully implement lean warehousing principles, businesses should follow these steps:
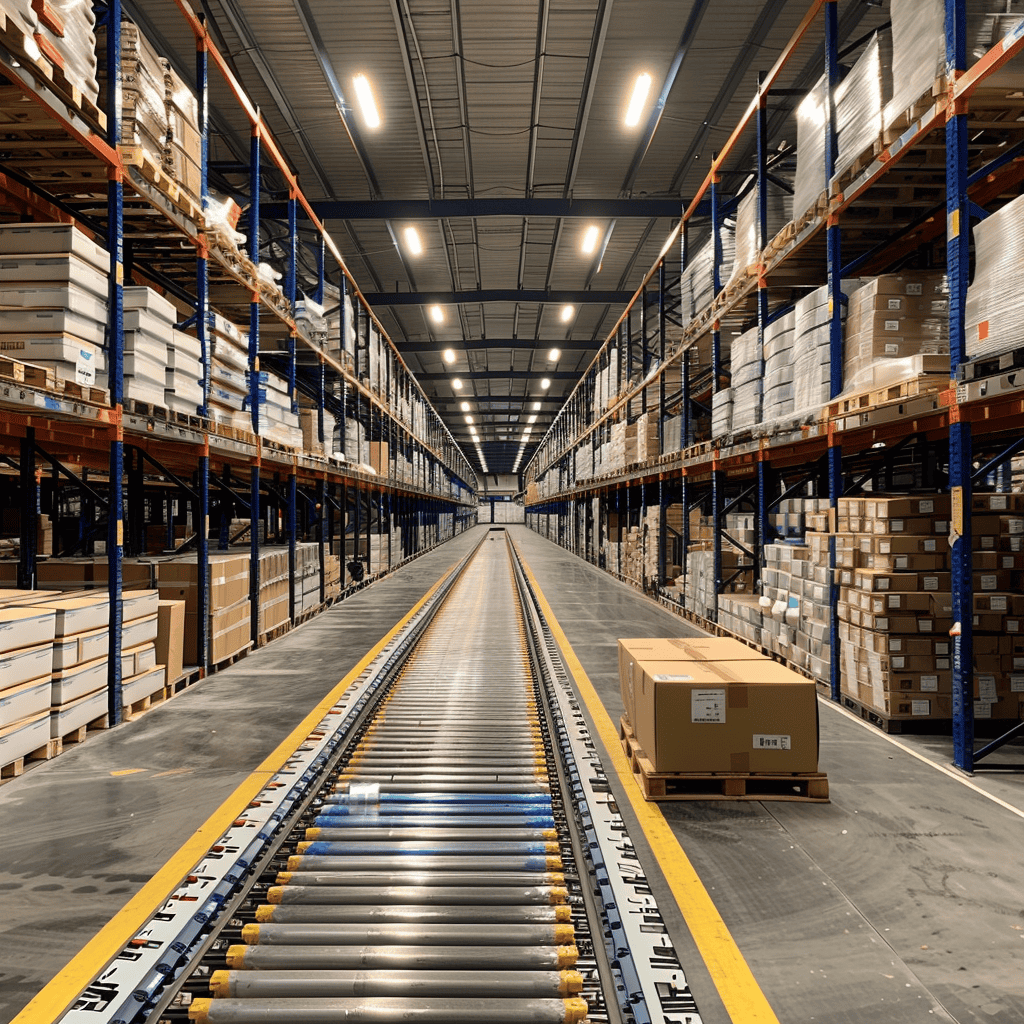
- Audit Warehouse Processes: Conduct a thorough audit of current warehouse processes to identify areas of waste and inefficiency.
- Implement 5S System: Apply the 5S principles to organize and maintain the warehouse environment.
- Integrate Technology: Invest in technology such as WMS and automation to streamline operations and reduce manual labor.
- Train Employees: Provide regular training to ensure all employees understand and adhere to lean warehousing principles.
- Foster a Culture of Continuous Improvement: Encourage employees to participate in identifying and implementing improvements.
Questions and Answers
What is lean warehousing?
Lean warehousing is a systematic approach to managing warehouse operations with the goal of reducing waste, improving efficiency, and enhancing productivity. It is based on lean manufacturing principles, which focus on streamlining processes, optimizing resources, and continuously improving operations.
What are the core principles of lean warehousing?
The core principles of lean warehousing include the 5S system (Sort, Set in Order, Shine, Standardize, Sustain), technology integration, continuous improvement, adopting best practices, and fostering employee involvement. These principles aim to create an organized, efficient, and productive warehouse environment.
What is the 5S system in lean warehousing?
The 5S system is a set of principles designed to organize and manage the warehouse environment to improve efficiency and reduce waste. The five principles are:
- Sort (Seiri): Remove unnecessary items to free up space and reduce clutter.
- Set in Order (Seiton): Organize items so they are easy to find and access.
- Shine (Seiso): Maintain a clean and well-organized warehouse.
- Standardize (Seiketsu): Establish consistent processes and procedures.
- Sustain (Shitsuke): Continuously maintain and improve the first four principles.
How does technology integration benefit lean warehousing?
Technology integration in such warehousing automates time-consuming activities and minimizes manual processes. Key technologies include Warehouse Management Systems (WMS) and automation and robotics. These technologies provide better visibility into operations, reduce errors, optimize storage, and improve order fulfillment processes.
What are the benefits of lean warehousing?
Implementing these warehousing principles offers numerous benefits, including reduced operational costs, improved efficiency, enhanced customer satisfaction, better space utilization, and higher employee morale. These benefits result from eliminating waste, streamlining processes, and fostering a culture of continuous improvement.
How can businesses implement lean warehousing?
To implement lean warehousing, businesses should follow these steps:
- Audit Warehouse Processes: Identify areas of waste and inefficiency.
- Implement the 5S System: Organize and maintain the warehouse environment.
- Integrate Technology: Invest in WMS and automation to streamline operations.
- Train Employees: Ensure all employees understand and adhere to lean warehousing principles.
- Foster a Culture of Continuous Improvement: Encourage ongoing participation in identifying and implementing improvements.
What are some best practices in lean warehousing?
Best practices in lean warehousing include cross-docking (direct transfer of goods from incoming to outgoing shipments), inventory management (regularly re-evaluating inventory levels and implementing a just-in-time system), and utilizing lean tools (5S, Kaizen, Value Stream Mapping) to identify and eliminate waste in the warehouse.
Conclusion
Lean warehousing offers a powerful approach to optimizing warehouse operations by reducing waste, improving efficiency, and enhancing productivity. By integrating the core principles of lean warehousing, adopting best practices, and fostering a culture of continuous improvement, businesses can achieve significant cost savings, better space utilization, and higher customer satisfaction. Implementing lean warehousing is not a one-time effort but a continuous journey towards operational excellence.